Thick-Copper PCBs
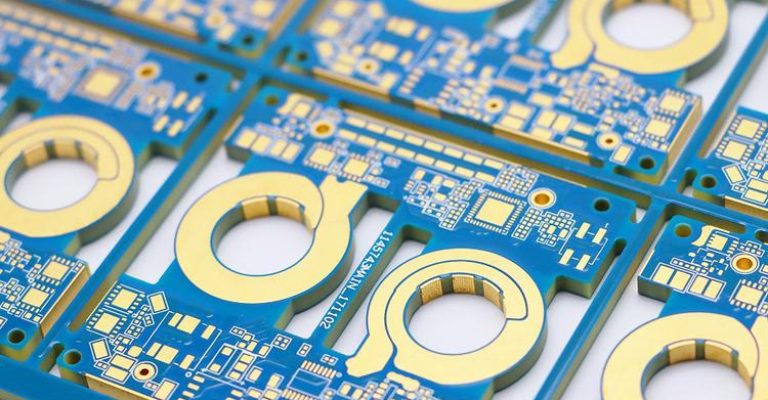
Thick copper pcb is a special type of circuit board developed in the electronic manufacturing industry to meet the requirements of high current carrying capacity and high thermal conductivity.
Compared with traditional thin copper circuit boards, thick copper PCBs significantly improve the current carrying capacity and heat dissipation performance of circuit boards by increasing the thickness of copper foil, making them an ideal choice for high-power electronic devices and special application fields.Providing stable and reliable current transmission and heat dissipation solutions for electronic devices .
Product Showcase
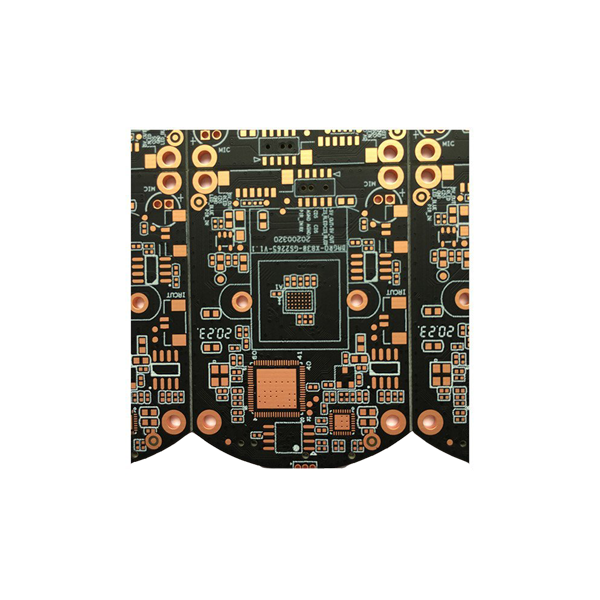
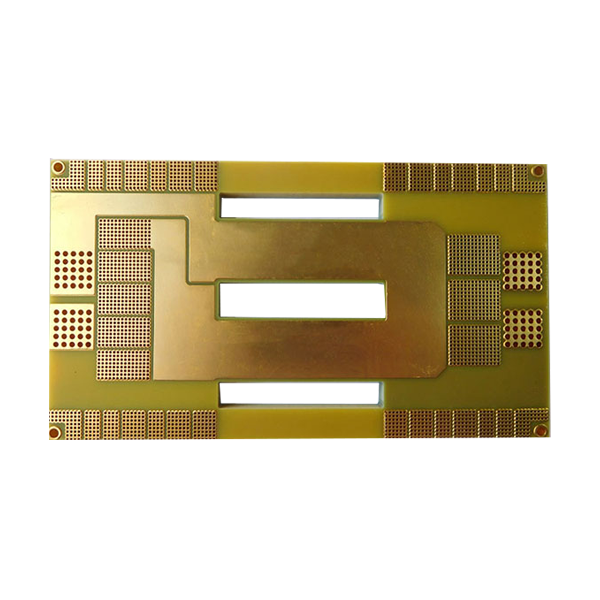
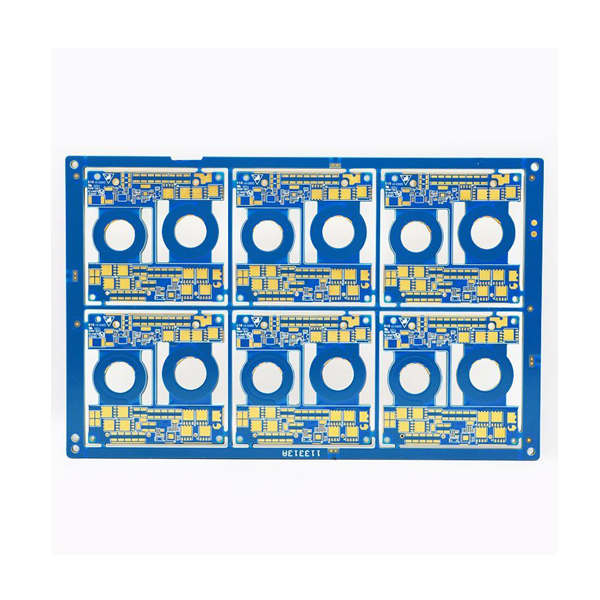
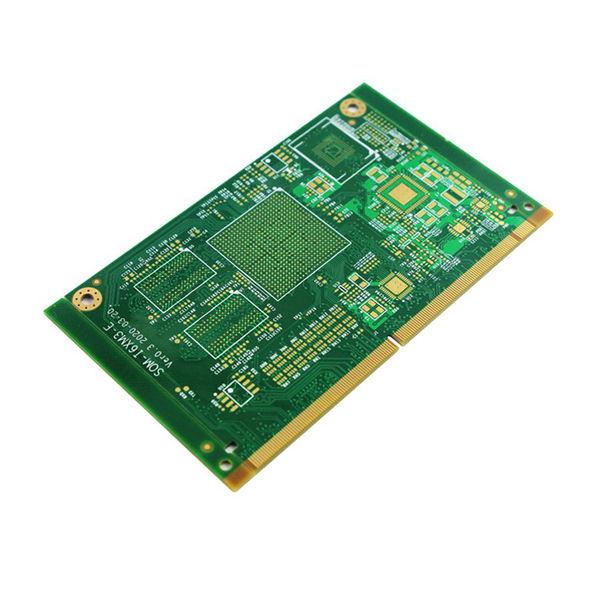
Capabilities
Capability | Parameter |
---|---|
Material |
FR-4 Standard Tg 140°C FR4-High Tg 170°C |
Min.Track/Spacing |
For External Layers: 4oz Cu 9mil/9mil 5oz Cu 11mil/11mil 6oz Cu 13mil/13mil 12oz Cu 20mil/32mil For Internal Layers: 4oz Cu 8mil/12mil 5oz Cu 10mil/14mil 6oz Cu 12mil/16mil 12oz Cu 20mil/32mil |
Min Hole Size | 10mil |
Max Outer Layer Copper Weight(Finished) | 15oz |
Max Inner Layer Copper Weight | 12oz |
Board Thickness | 0.6-6mm |
Surface Finishing |
HASL Lead Free Immersion Gold OSP Hard Gold Immersion Silver Enepig |
Solder Mask | Green,Red,Yellow,Blue,White,Black,Purple,Matte Black,Matte Green |
Silkscreen | White,Black |
Via Process |
Tenting Vias Plugged Vias Vias not covered |
Testing |
Fly Probe Testing (Free) AOI Testing |
Build Time | 5-10 Days |
Lead Time | 2-3 Days |
Are you looking for a high-quality and full-range PCB fabrication, PCB assembly?
FAQ
Thick copper printed circuit board refers to a printed circuit board with copper foil thickness far exceeding conventional standards.
Their main purpose is to meet the requirements of high current density, high thermal conductivity, and high mechanical strength.
This type of circuit board is commonly used in fields such as power electronics, automotive electronics, industrial control, communication base stations, and aerospace to ensure stable operation in high-power and harsh environments.
The thickness of copper foil for thick copper PCBs can be customized according to specific application requirements, but it is usually several times or even tens of times thicker than conventional copper foil.
The common thickness range for thick copper PCB copper foil is from 1 ounce per square foot (about 35 microns) to 10 ounces per square foot (about 350 microns), and some special applications may even require thicker copper foil.
Manufacturing thick copper PCBs requires a series of special processes and technologies, including high-precision copper foil cutting, special etching processes, laser drilling, high-precision electroplating, and multi-layer board lamination.
Due to the increase in copper foil thickness, these processes and technologies need to be adjusted and optimized accordingly to ensure the electrical performance, mechanical strength, and heat dissipation performance of the circuit board.
Thick copper PCBs have significant advantages in high-power applications.
Firstly, they can carry higher current density, reduce resistance and heat generation, and improve energy efficiency.
Secondly, the thick copper layer has good heat dissipation performance, which can quickly conduct heat to the surrounding environment and prevent electronic devices from overheating.
In addition, thick copper PCBs also have higher mechanical strength and stability, which can withstand the mechanical stress caused by high current and high temperature.
Ensuring the quality and reliability of thick copper PCBs requires multiple approaches.
Firstly, selecting high-quality raw materials and advanced manufacturing processes is the foundation.
Secondly, strict quality control and testing are carried out during the manufacturing process, including electrical performance testing, mechanical strength testing, thermal cycling testing, and reliability testing.
In addition, customized design and optimization are needed based on specific application requirements to ensure that the circuit board performs well in practical applications and meets customer expectations and needs.