BGA Assembly
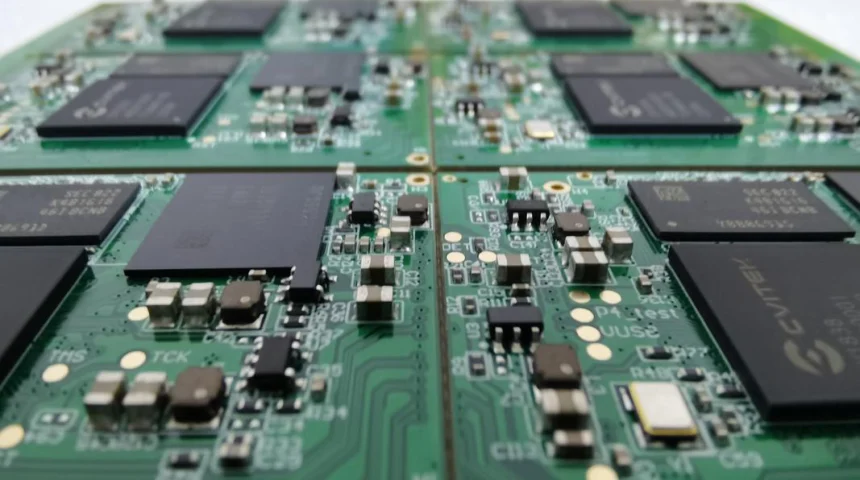
BGA technology achieves more compact and reliable circuit connections by designing an array of metal balls at the bottom of the integrated circuit package as electrical connection points, which are connected to corresponding pads on the printed circuit board.
In the BGA Assembly manufacturing process, the first step is to accurately place the BGA packaged IC on the predetermined position of the PCB.
The advantage of BGA Assembly manufacturing technology is that it can provide higher circuit density and better electrical performance, while reducing the size and weight of circuit boards.
Product Showcase
Capabilities
BGA assembly service is one of the many service types we offer. FAST TURN PCB can provide you with high-quality and cost-effective BGA assembly for your PCBs. The minimum pitch for BGA assembly that we can accommodate is 0.14mm 0.2mm. We offer PCB fabrication and assembly services containing the following BGA types:Plastic BGA (PBGA)、Ceramic BGA (CBGA)、Micro BGA、Micro Fine Line BGA (MBGA)、Stack BGAs、Lead BGA and leadless BGA.
Are you looking for a high-quality and full-range PCB fabrication, PCB assembly?
FAQ
Compared with the previous packaging technology, the thickness and weight are reduced; the parasitic parameters are reduced, the signal transmission delay is small, and the frequency of use is improved; the assembly can be coplanar welding, with high reliability, excellent heat dissipation capacity, electrical characteristics, and high-efficiency system. Product compatibility.
Increase in density
BGA Assembly involves the use of more solder balls. This causes an increase in the connection between these balls. The connection leads to an increase in the density of connections. Also, these numerous solder balls present reduce the space available on the circuit board. This leads to lighter and smaller products.
Better electrical performance
BGA Assembly offers better electrical performance. This quality is due to the shorter path between the circuit board and the die. BGA assembly dissipates heat often due to its tiny size. Also, this package lacks pins, which can easily bend and break, increasing its electrical performance and stability.
Improved heat dissipation
BGA Assembly ensures improved heat dissipation. It possesses this quality due to its low thermal resistance and tiny size.
Self Alignment
The PCB space is well utilized. This is because the soldering balls usually self-align underneath the board. BGA Assembly ensures the use of the entire circuit board.
Solder joints are very complex and have irregular shapes. Therefore, checking the quality by visual inspection would take time and effort. Thus, for more complex issues, it’s advisable to use X-ray imaging. Let us consider both methods.
Visual Inspection (Optical Inspection)
This method for checking solder joint quality is only effective for detecting defects. These include closed circuits, the absence of solder in joints, and more. The method is straightforward because you only need the naked eye to inspect.
X-ray Inspection
This method detects bridging, incomplete wiring, voiding, and other defects. Also, it can detect majority of defects on leads and pads.
This method involves inspecting the solder joints using an X-ray device. The X-ray machine is composed of the X-ray source and detector. Both are connected to the system and used to transfer the image to a screen. X-ray inspection is fast and automated, thereby saving time.
The process of BGA Assembly deals with the mounting and soldering the BGA components on PCBs. Here are the steps:
PCB Design and Preparation
This step involves preparing printed circuit boards. The process is possible by applying solder paste to pads where the BGA mounting will happen.
Solder Paste Application
This step involves the application of solder paste on the PCB metal pads through stencil printing. The stencil’s thickness helps determine the quantity of solder paste to use.
Components Placement
This step is also called the “Pick-and-place” step. The process describes how an automated machine picks and places the BGA components on the printed circuit boards. The machines usually rely on high-quality cameras. This is to ensure the accurate placement of the components.
Reflow Soldering
Here, a reflow oven helps to heat the board. The reflow oven melts the solder paste. This causes a strong bond between the circuit board and the BGA components.
Inspection and Testing
Due to the physical structures of the BGA components, visual inspection won’t work. Therefore, an X-ray inspection helps to check soldering defects. These defects include short circuits, voids, air holes, and more.Electrical tests help to find defects like short and open circuits.